Our partnership with Xemelgo, the cloud manufacturing experts, produced the roll-out of an RFID visibility solution that combined the Internet of Things (IoT), artificial intelligence (AI), mobile, and cloud technology to enable transparent asset tracking. This revolutionary IoT asset tracking system, dubbed the Xemelgo X-track System, works in tandem with our Brady® CenSys Readers and other RFID reader solutions to provide a bird’s eye view of tagged assets as they move throughout your factory floor.
Cloud manufacturing is an affordable and easy-to-set-up solution for managing work orders, work in process, and inventory fluctuations. The Xemelgo tracking software is at the forefront of modernizing manufacturing using Industry 4.0 solutions. To understand this newest phase of the industrial revolution, think about how quick and easy access to real-time data could aid your business:
• Keep tabs on real-time inventory totals to fulfill orders on time
• Remove human errors—Data entry errors, data analysis errors, misplaced and lost assets
• View up-to-the-minute historical data without wasting time running reports
• Learn when important orders will ship with increased visibility on your factory floor
• Bid on new business armed with the knowledge of your true costs
• Avoid the learning curves associated with Enterprise Resource Planning (ERP) tools
Xemelgo’s enhanced suite of solutions offers a smart manufacturing portfolio of apps that accomplishes all of these tasks and more. And they are fully customizable to fit your industry and needs. Expedite work order and asset tracking, with the ease of cloud, mobile, AI, and IoT computing. New enhancements include inventory and shipping features that work seamlessly with a variety of RFID tags (Which tags are right for your business? Get answers at our RFID FAQs page).
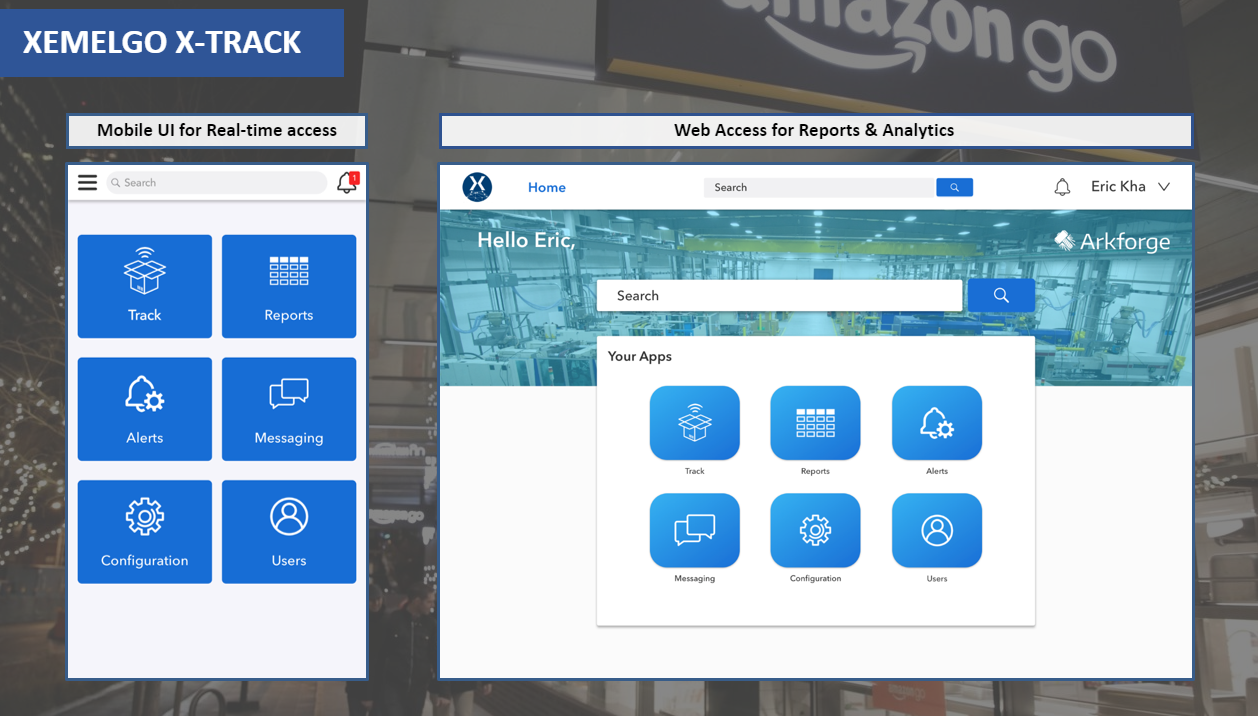
The Xemelgo groundbreaking mobile user interface (UI) apps deliver real-time access with smartphones—Get text notifications for preset alerts and access the web to track, run reports, message, and determine users. This state-of-the-art blend of internet technologies not only empowers you to view a virtual representation of asset storage and work order status—It also provides an unparalleled collaboration platform to discuss and approve work orders to ensure on-time delivery.
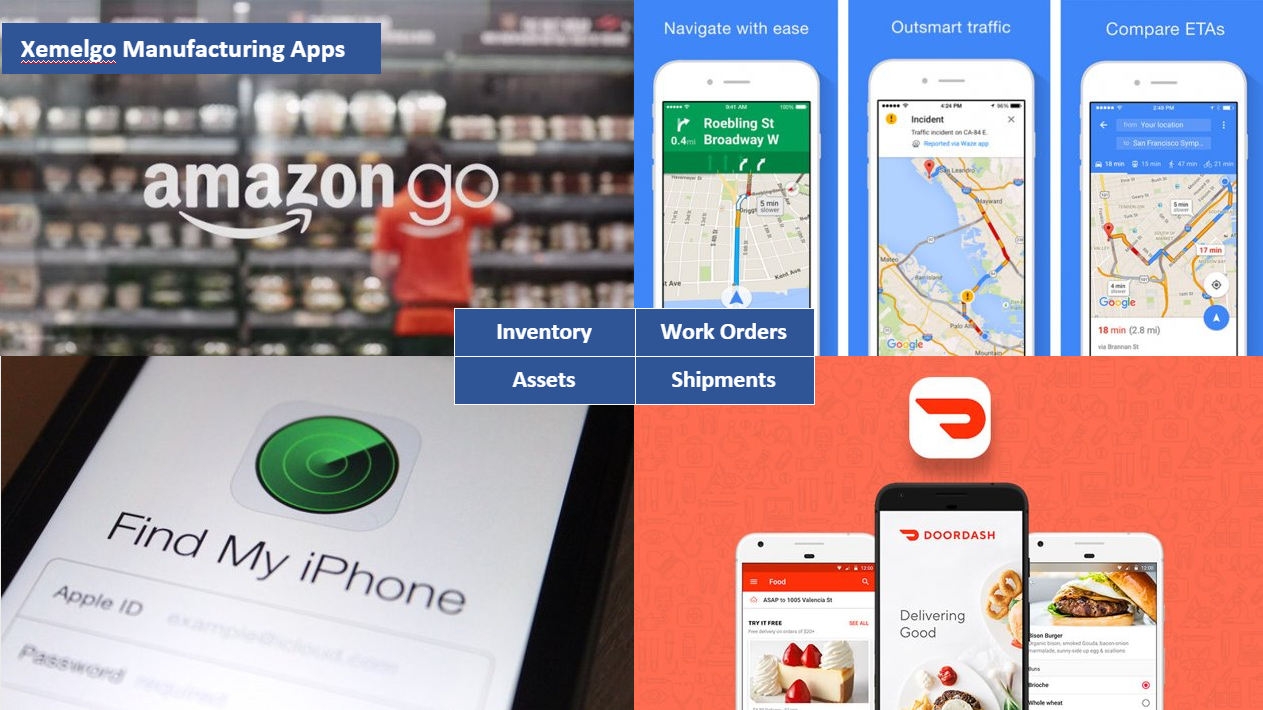
The beauty of the Xemelgo X-Track suite of software apps is that it provides all-in-one real-time asset tracking and process visibility in your workplace:
Track assets with the same ease as the Find My iPhone app
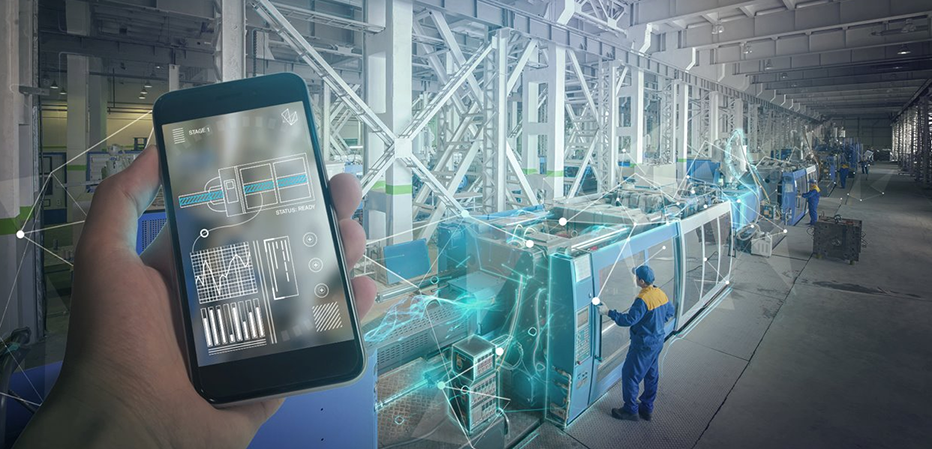
Sign into the cloud and oversee locations of your tagged assets. Once data is collected from readers placed strategically throughout your factory, you can pinpoint on a map of your facility where a tagged object is currently located, and where it was last seen in the same way that you can track your iPhone from another device.
Find work orders with the same ease as finding a location on Google Maps
Navigate progress as if using Google maps for your factory, allowing you to determine any slowdowns and bottlenecks, rerouting the progress from inception to completion, and determining a final ETA. Complete backlog visibility is under your control as you receive real-time movement notifications of work in process (WIP).
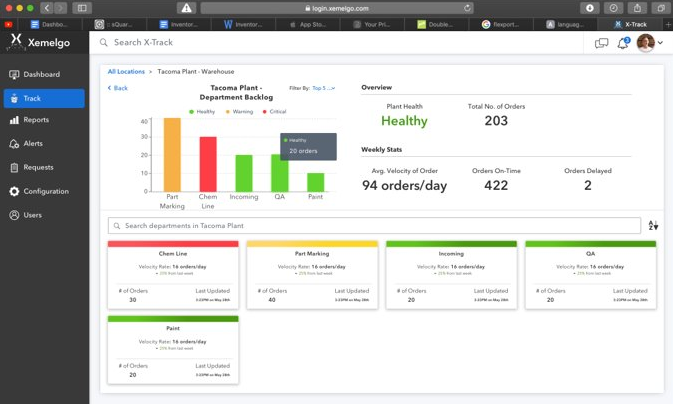
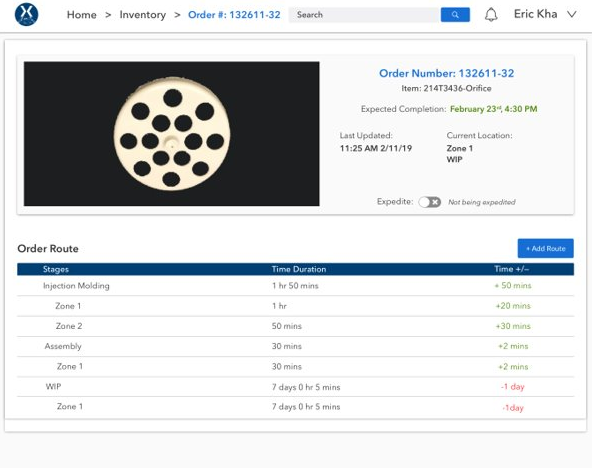
NEW! Xemelgo’s real-time inventory management module delivers up-to-the-minute inventory overviews plus the same kind of smooth product and part location experienced with the AmazonGo app
Inventory status is automatically updated as items are moved and shipped, while real-time alerts sound the alarm when items are overstocked or drop below minimal thresholds. Receive inventory management recommendations automatically: order lists for hot items that frequently ship and lists of items that are in low quantity and need replacement ordering to prevent empty shelves. Easily tap into purchasing systems to update orders on your mobile phone or device.
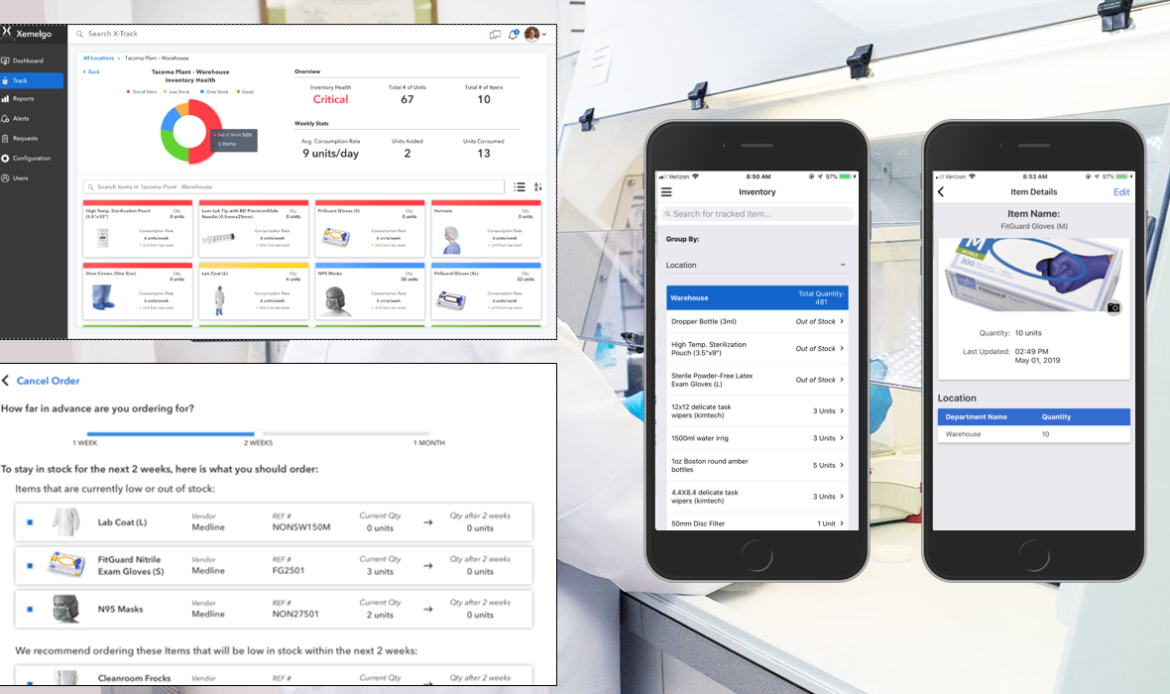
Track adhesives, paints, and other chemical supplies used in manufacturing, and track assets that are pulled from storage containers, used, and then returned to storage with Xemelgo’s inventory management module. Even track expiring chemicals and tools. Size is of no consequence: IDI offers small hardened RFID tags that can be applied to small calibrated tools with 2-10 foot read ranges to help track usage and help save wasted hours of time searching for lost tools in your facility.
NEW! Xemelgo’s real-time shipment tracking module is similar to the DoorDash food delivery app
Track the delivery of tagged items between buildings and receive a delivery ETA and arrival confirmation. Xemelgo’s app creates a map view of the real-time tracking of parts and shipments between buildings, warehouses, and facilities. Just like meal delivery with DoorDash, information is captured when Items leave one location and arrive at the next.
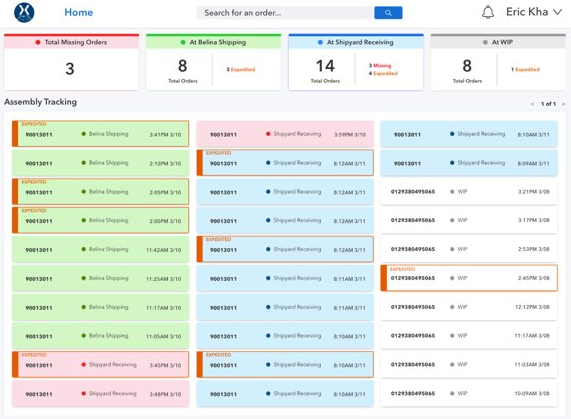
How do forward-thinking companies put this powerful suite of Xemelgo tracking and management modules into real-life use?
Xemelgo goes to work for tracking supplies in a compounding pharmacy. Some supplies, such as booties, are critical to retaining a cleanroom environment. Xemelgo apps keep track of the booties by functioning like AmazonGo. Employees place RFID tags on boxes of booties (or other necessary supplies) and place the CenSys RFID Reader at the door to automatically keep track of inventory. The manager sets a threshold for a low inventory alarm to notify by text, email, or both. When tracked stock supplies get low, mobile users receive a warning to reorder. Additionally, mobile users also have the ability to track stock over a period of time to understand the frequency of how often particular supplies are depleted and how many they go through before ordering. This predictive knowledge prevents overstock and out-of-stock situations.
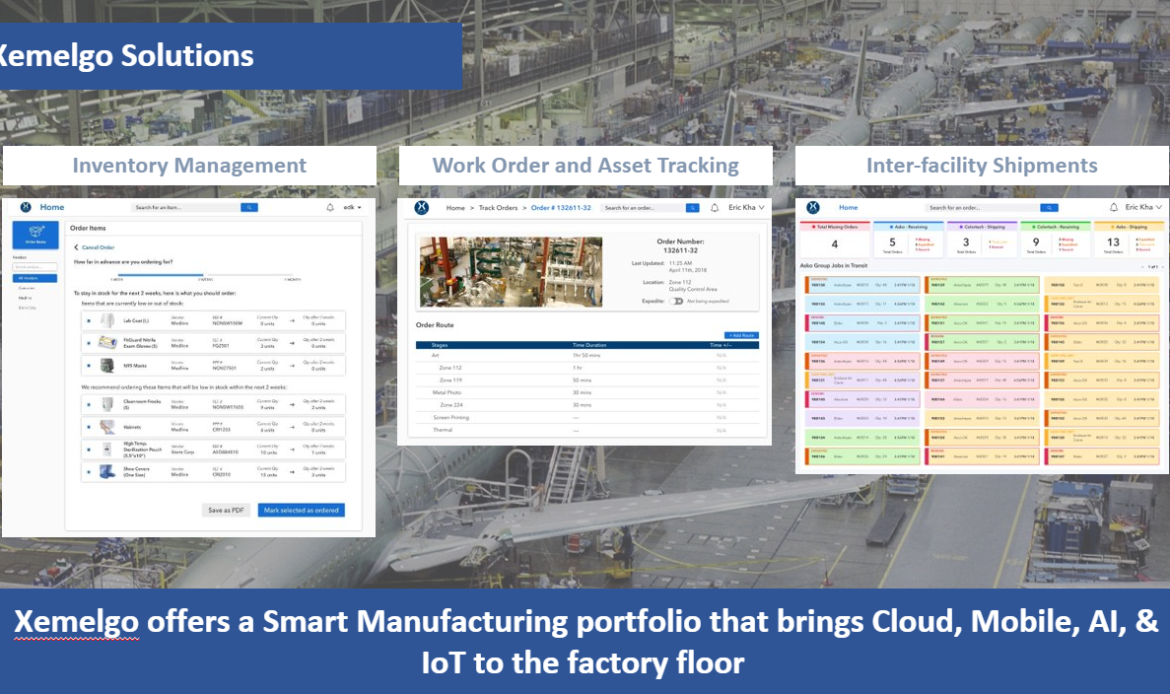
Real-time inventory knowledge, without the need of laboriously entering data, running time-consuming reports, and analyzing disparate data takes a simple combination of easy-to-install, fixed CenSys RFID readers and handheld Bluetooth enabled RFID readers. And this is what cloud manufacturing is all about—Breakthrough communication for Industry 4.0 advancement.
The use of personal cell phone use and automated alerts are ways to quickly use data to determine changes in your business environment and act on them in a timely manner. When mobile devices and RFID tech communicates with each other, as well as human decision-makers, we’ve entered a world of technology that allows for streamlined ways to solve and avert problems. Imagine the possibility of zero downtime in production.
Also, imagine the possibilities of customization. Xemelgo opens the door to customized mobile reports delivered as newsfeeds, bookmarking the most important charts to remain in your feed, share charts easily with other users, and dig deeper in reports for further analysis. It’s all at your fingertips.
Gaze into the crystal ball of Industry 4.0. What does the future hold? The hope is that piece parts (small as screws/fasteners) will be tracked with the assistance of a digital Wi-Fi scale, vision sensors, and RFID to gain even more visibility on the smallest parts. That’s one example. What is your vision? Our in-house cloud manufacturing consultants can make your vision become reality. Contact us at 425-438-2533.